- HOME
- Research and Development
- R&D Organization
- Research Laboratories
- Composite Materials Research Laboratories
Composite Materials Research Laboratories
The Laboratories dated from 1990, unifying the Ehime Research Laboratory of the Fibers and Textiles Research Laboratories and the Composite Research Laboratory of the Polymer Research Laboratories. Research targets the carbon fiber TORAYCA™, matrix resins and other composite materials, fabric, prepreg and other intermediate materials, composite materials processing, design and analysis.
The Composite Materials Research Laboratories conducts advanced and vertically integrated R&D activities from carbon fibers and matrix resins to composite materials.
Carbon fibers
By establishing new technologies enabling precise control of carbon crystalline structure, we have commercialized T800S carbon fiber with high strength and high modulus. This fiber has been used in major aircraft in recent decades such as Boeing 777 and 787, and Airbus A380. Further development of these cutting-edge structure control technologies has allowed us to commercialize our latest TORAYCA™ carbon fiber, T1100G featuring a 10% improvement in both strength and modulus. We are committed to continuing our carbon fiber R&D activities, and thereby to creating higher performance carbon fibers.
Airbus A380 using TORAYCA™ carbon fiber
Boeing 777X, a next generation, large-scale aircraft, which is under development
(Toray is scheduled to supply TORAYCA™ prepreg) ©Boeing
Matrix resins and prepregs
Our interlayer toughening technology, using thermoplastic particles in interlayer regions of laminated prepreg sheets, improves impact resistance. This approach has allowed us to commercialize TORAYCA™ prepreg T800H/3900-2 the first carbon fiber material qualified (in 1990) for primary structures of Boeing’s civil transport aircraft, and used in Boeing 777 aircraft. We have also developed NANOALLOY™ technology, enabling both the high strength and high impact-resistance of composites.
Development of TORAYCA™ T1100G with high tensile strength and high modulus
Composites
We have developed innovative resin transfer molding technologies enabling high-cycle molding of automobile parts in less than 10 minutes. In addition, we have developed innovative press molding materials enabling molding of high strength parts in less than one minute. These are some of our efforts to develop carbon fiber reinforced composite technologies for full-scale automotive structural components through a number of national projects since 2003. We have also developed TORAYCA™ prepreg ET40, drastically improving formability compared to conventional prepregs while maintaining good mechanical properties, and CFRF with a 3D network structure of carbon fiber enabling ultra-light-weight and high rigidity.
Composite materials which achieve superior formability and mechanical properties simultaneously
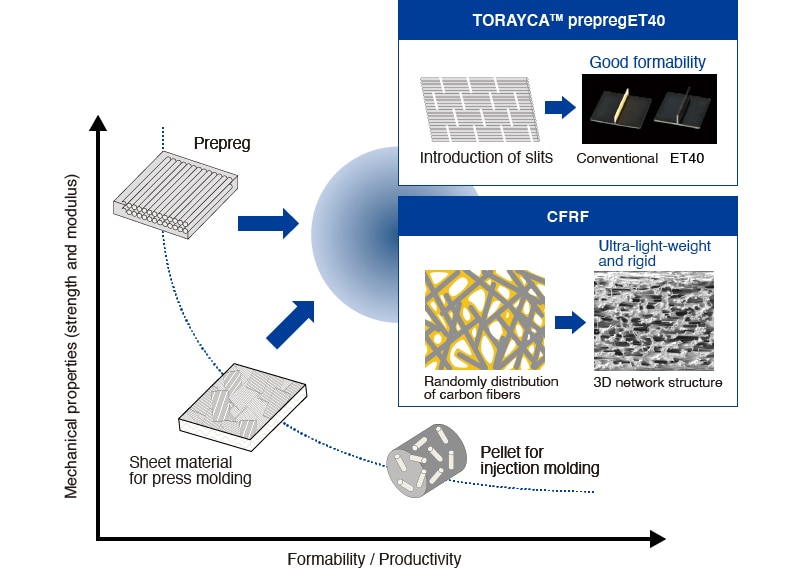
* ET40 is winner of the Technology Award of the Japan Society of Composite Materials in 2015
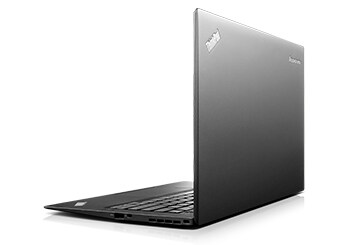
Plastic materials reinforced with carbon fiber filaments are used in lightweight and high rigidity
PC chassis.
* Winner of the Prime Minister Prize of National Commendation for Invention in 2008
Photo:Lenovo (Japan) Ltd.
Milestones in Toray R&D
1971 | Commenced production of TORAYCA™ carbon fiber. |
---|---|
1977 | Established Ehime Research Laboratory of the Fibers and Textiles Research Laboratories. |
1987 | Established Composite Research Laboratory of the Polymer Research Laboratories. |
1990 | Established Composite Materials Research Laboratories. |
1992 | Commenced production of TORAYCA™ carbon fiber prepreg T800H/3900-2 for use as primary structural material in civil aircraft. |
1996 | Commenced production of carbon-fiber-reinforced PC chassis with superior electromagnetic wave shielding properties. |
2003 | Developed super-lightweight and high rigidity PC chassis. |
2008 | Developed high-cycle molded components for automobiles. |
2011 | Boeing 787 using Toray CFRP came into service. |
2014 | Commenced production of high strength and high modulus TORAYCA™ carbon fiber T1100G. |
2017 | Developed next generation TORAYCA™ carbon fiber prepreg T1100G/3940 for aircraft and space applications. |