#10
Life and breath: innovative fabrics on the frontline against disease
The need to protect health workers operating in hazardous conditions has led to remarkable innovations in the development of biohazard gear. Advanced fabric technology is now helping to protect the lives of those who save them.
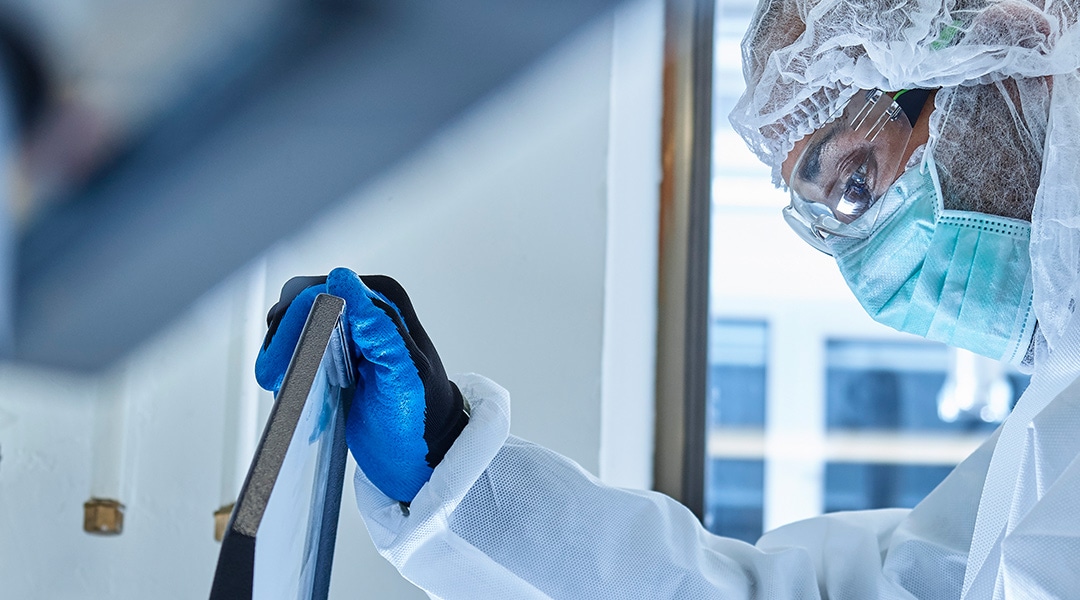
The Ebola outbreak that erupted in West Africa in 2013 posed a daunting challenge to health workers battling to contain the epidemic. In addition to risking their lives while treating the victims of this terrifying disease, medical personnel also had to contend with protective gear that induced “a feeling of suffocation.”
In a tropical climate, heat inside the all-encompassing biohazard suits quickly soared above 115°F: “After about 30 or 40 minutes, your goggles have fogged up; your socks are completely drenched in sweat,” noted one doctor. “You’re just walking in water in your boots.”
Two years into the crisis, Toray went to Guinea, the outbreak’s epicenter, to test a new biohazard fabric developed to cope with extreme heat and humidity. Called LIVMOA™, the biohazard gear aimed to reconcile the needs of safety and comfort on the frontline of the deadliest of epidemics. Its unique advantage is a non-woven material that prevents deadly microbes from entering, while allowing heat and moisture to filter out.
Responding on a global scale
The need for such technology was urgent. Just months into the Ebola crisis, the deaths of more than 200 health workers battling the disease underscored how secure, comfortable biohazard gear was a crucial piece of the eradication puzzle – prompting then US President Barack Obama to launch a global initiative to develop better protective suits.
“The urgent need for clear standards for personal protective equipment use became acutely apparent during the unprecedented outbreak of Ebola virus disease in certain western African countries in 2013-16,” the World Health Organization said.
In Guinea, Toray carried out tests of the LIVMOA™ protective suit at Donka Hospital in the capital Conakry, under simulated Ebola-fighting conditions. Trials showed the gear to reduce relative humidity within the suit by more than 30 percent compared to standard protective suits – allowing medics to work longer and more effectively. Studies also showed the suit to increase breathability by more than 96 percent. Feedback from health workers was overwhelmingly positive.
“In anti-infection garments, the barrier properties of blood and viruses generally decrease as moisture permeability increases, but these apparently contradictory objectives become compatible by applying our unique material,” Toray says.
The LIVMOA™ infection-control suit features a three-layer structure in which non-woven polymer sheets are placed on each side of a special porous film. The microscopic pores of this functional film are wide enough to let out steam yet tiny enough to block microbes. In addition, non-woven polymer material confers strength to the fabric, allowing it to be used as anti-infection protective wear. These factors allow LIVMOA™ to resolve the seemingly divergent objectives of moisture permeability and hermetic protection.
Feedback from the health workers testing the suit allowed Toray to make improvements, including ease of putting on and removing the gear – a key factor since many Ebola fighters were infected during the complicated procedure of taking off protective garments. The design also incorporated suggestions to make the appearance of the suit more reassuring, an important consideration as many stricken patients had been frightened of doctors in heavy protective gear. The suits are disposable – slated for destruction after each use – meaning health workers have the assurance of working in a sterile environment for every tough assignment.
Safety across many sectors
LIVMOA™ is designed for a wide array of challenging endeavors, such as working in oil refineries and handling hazardous chemicals, fighting pathogens and carrying out biotech research – demonstrating the versatility of the non-woven technology.
For example, Toray developed a sterile version of the LIVMOA™ garment with Japan’s Foundation for Biomedical Research and Innovation at Kobe (FBRI) – a center led by Nobel Medicine laureate Tasuku Honjo – to support research into regenerative medicine, a branch of medicine that develops ways to replace damaged cells, tissues and organs. The sterile suit captures microscopic impurities that might contaminate research.
Toray applied a special fabric called TORAYMICRON™ that captures airborne particles to create pristine laboratory conditions. In tests, the technology achieved 98 percent less dust-generation compared to other sterile suits.
Meanwhile, the chemical version of the LIVMOA™ suit is used for potentially dangerous tasks such as asbestos removal and polyurethane spraying. In January, Toray received EU certification for the chemical-protection suit, setting it up for launch in European and US markets.
These are just a few of the applications of the innovative LIVMOA™ fabric. And Toray’s infection-control clothes are also emblematic of the company’s mission to support global development. Toray donated 10,000 LIVMOA™ biohazard suits to the Guinean government after the successful trials at Donka Hospital. The garments are being used in sensitive health and sanitation work, in addition to being on standby for infectious disease emergencies. The LIVMOA™ protective suit has also been deployed in hospitals in Nigeria and universities in Japan, with full-scale global commercialization planned in the near future.
Saving lives in health crises means protecting the lives of heroes in the field. Unique materials – leveraging advanced chemical research – can breathe life in the face of deadly challenges.